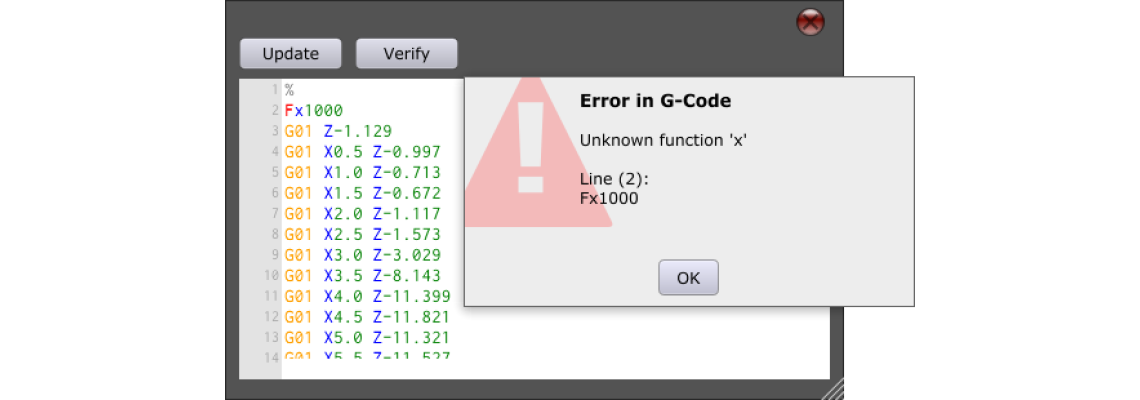
There are several common errors that can occur in CNC programming, some of which include:
Syntax errors: These occur when the program contains incorrect or invalid commands, and the machine is unable to execute the program.
Toolpath errors: These occur when the toolpaths are not properly generated, resulting in the cutting tool moving in an unexpected or incorrect manner. This can cause the tool to collide with the workpiece or machine, or result in poor surface finish or dimensional accuracy.
Over-travel errors: This occurs when the machine exceeds its maximum travel limits, which can cause the machine to crash or damage the workpiece.
Tool wear or breakage: This occurs when the tool is worn out or broken during the machining process, which can cause the machine to stop or produce poor quality parts.
Incorrect speeds and feeds: This occurs when the machine is set to the wrong speeds and feeds, which can cause the tool to wear out quickly, produce poor surface finish, or break.
Misaligned or clamped workpiece: This occurs when the workpiece is not properly aligned or clamped, which can cause the machine to produce parts that are out of tolerance or cause crashes.
Wrong tooling or accessories: This occurs when the wrong tooling or accessories are used for a specific machining operation, which can cause the machine to produce poor quality parts or stop.
Alarm: This occurs when a specific alarm is triggered by the machine, which indicates that something is wrong with the machine or the program.
Leave a Comment